Exception Based Management for Wells
Project Description
Our customer was facing a significant growth in well count with no chance of matching that with similar increase in staff. Increased efficiency in well management and opportunity value realization was required. EBS and Lean were the selected approach.
Each asset team spending 30-120 mins per day identifying Well problems.
Analysis of ESP problems take 25 mins and repeated by 3 disciplines with no clear ownership
Well count growing from 4,500 to 9,000 in 10 years
Achieved Business Benefits
98% of 7,500 wells of 12 different types are monitored by EBS
Employee survey results show saving of 40% of PE and OPS staff time through semi automated Nibras Lean-EBS process workflows
Well count grew by 67% in 5 years but Engineers monitoring wells by only 33% (50 PEs saved)
Faster detection-of and value-realization from well problems and optimization opportunities leading to 5% extra production
30,000 bpd of hidden deferment made visible by semi-automated workflow of well deferment booking
SOPs (Standard Operating Procedures) improved quality of well monitoring
Tags
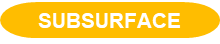


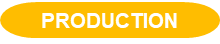
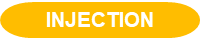
The Tool
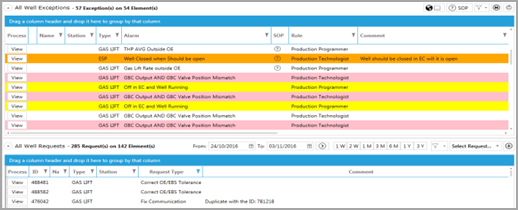
Standard Exception Viewer prioritizes work of an individual based on value
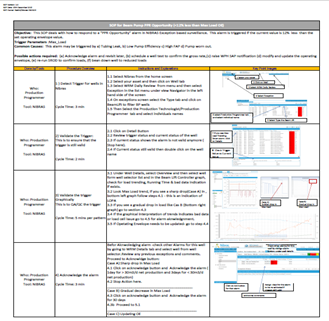
SOPs guide engineers how to address each exception to a min. standard regardless of experience level.
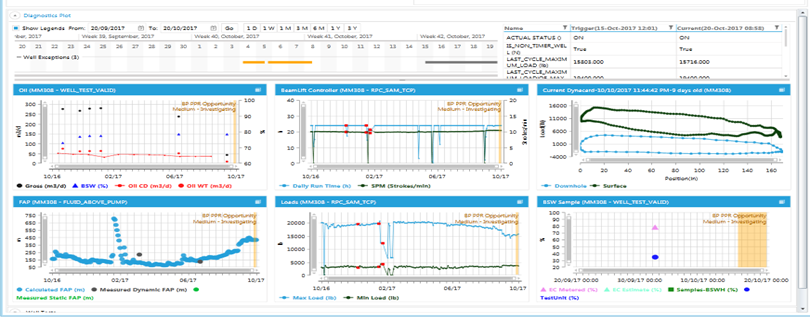
Standard Diagnostic Plots (per well-type) to establish root-cause and remediation action
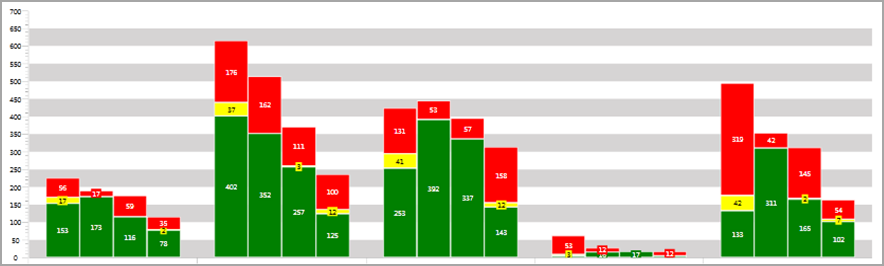
Andon board shows exception handling performance across different assets, well types or roles

7,500
Wells (12 types) monitored by Exception

25 FTEs
25 fewer PE required to monitor increased well count

40%
PE time spent on data down from 53% to 14%

5%
Extra production